Circularity in concrete & cement
Concrete and cement repair, reuse, recycling and downcycling
Concrete is one of the most used materials in the world [i].
Unlike steel, concrete is a composite material and consists out of gravel or crushed stone (≈41%), sand (≈26%), water (≈17%), cement (≈11%) and air (≈6%) [ii] which makes it more difficult to break down into its individual components.
​
The lion's share of the emissions from concrete production comes from the manufacturing of one of its components - cement.
​
Each year, over 4 billion tons of cement are produced. The global cement production accounts for approximately 8% of global emissions [iii]. It is the second-largest industrial emitter of CO2 after iron and steel and 90% of its emissions are caused by the production of clinker [iv].
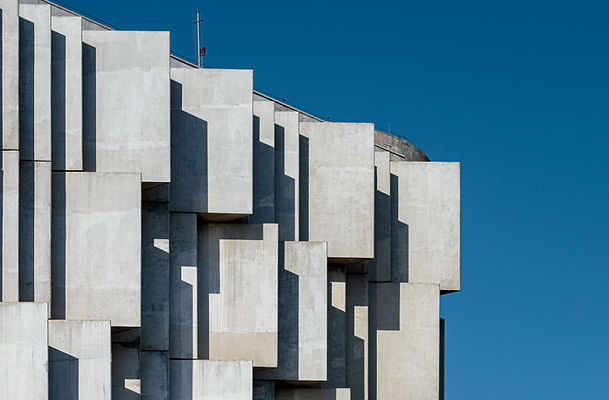
How can we reach a more efficient cement & concrete sector?
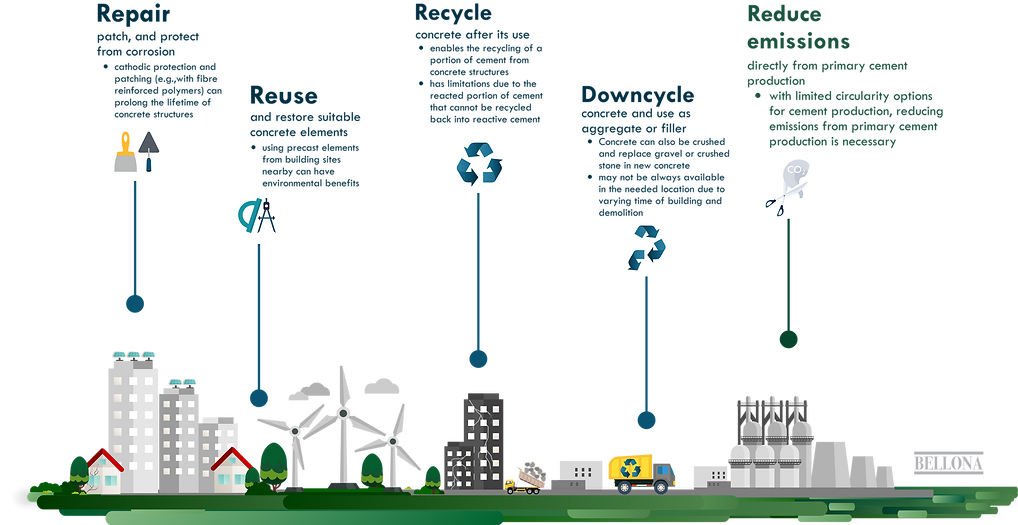
Repair and reuse
During a lifetime of use, buildings and infrastructure deteriorate. This deterioration shows in the form of cracking, fracturing, delamination and corrosion in the structure [v],[vi]. The deterioration of concrete materials can be slowed down by measures such as protection from corrosion (i.e., cathodic protection)[1] combined with patching of the deteriorated concrete with materials such as fibre reinforced polymers (plastics) [vii]. While this erosion of the physical properties of a structure can be slowed down with maintenance and repair, eventually the structure becomes unsuitable for use and needs to be disassembled.
​
After a building or piece of infrastructure is put out of use, parts of it may potentially be reused for new purposes [viii] in building sites nearby. Even though the process of returning existing concrete elements to use is complex, reusing precast concrete elements from construction sites in close proximity [2] has potential environmental benefits due to an assumed reduction in new concrete consumption [3].
​
Repair and reuse of concrete elements can increase their lifetime and contribute to the material efficiency of cement and concrete use.
However, each case needs to be assessed to ensure that the energy and material costs for the process don't outweigh the benefits of reusing or repairing concrete elements.
​
[1] Corrosion is one of the most common causes of deterioration of concrete reinforced with steel. It is also exacerbated by the absorption of CO2 into the concrete over the lifetime of the building or structure.
[2] Otherwise, the emissions from the transport of heavy concrete might outweigh the benefits of reusing existing concrete blocks and slabs.
[3] The reduction in concrete consumption needs to be proven with verifiable data and paired with a reduction in the production of new cement in the system.
Recycling
If concrete elements cannot be reused for a different purpose, they can be partially recycled to produce new concrete [ix]. Traditionally, concrete was only downcycled into smaller concrete granules which then couldn’t be used in the production of new concrete [x],[4]. However, breaking the concrete rubble through the weakest link (the cement stone) can isolate its different components and contribute to the production of new concrete. During the curing process, concrete chemically reacts when moving from a liquid to a solid state. This reaction is not complete, so some reactive cement may be recovered. The technology, developed by SmartCrusherBV, a company based in the [xi],[xii], can take concrete rubble and mechanically process it back into sand, gravel and reacted and unreacted cement. Some of these components can then be used in the production of new concrete.
​
Some unreacted cement can be recovered from old concrete, which can then directly substitute cement produced.
However, recycling is still associated with significant material losses and will therefore need to be complemented with the decarbonisation of primary cement production.
​
However, the cement recovered from the process can only be used to create new concrete if it hasn’t reacted to form solid concrete (i.e., hasn’t been ‘cured’). This means that during the recycling process of the cement is lost, either because it has already reacted or because of material losses. Due to these limitations, cement recycling still needs to be complemented with primary cement production. Therefore, at least half of the cement going into the production of new concrete will have to be produced through the conventional production process [xii].
​
[4] Currently, over 98% of downcycled concrete is used in road construction. Less than 2% is used as a substitute for sand or gravel used for new concrete production.
Downcycling
Downcycling takes place when the recovered concrete lacks the necessary characteristics to be re-used in similar structures or recycled to produce liquid concrete.
​
Crushing concrete and using it in different applications is a common practice in the construction and buildings sector today. When compared to recycling, downcycling of concrete is less complex and therefore more affordable and more common. Concrete can be crushed to a specific size and used as aggregate in new concrete structures [xiii]. Currently, aggregate made from downcycled concrete accounts for ~6% to 8% of aggregate use in Europe. Crushed concrete can also be used to build roads, building foundations [xiv], sidewalks [xv], erosion barriers [xvi] and other applications.
Downcycled concrete prevents landfilling, but doesn't influence the emissions from cement production since it meets demand for different application (e.g., road building).
​
​
However, this means that downcycling cannot replace concrete in all cases and that primary cement production to produce new concrete is still necessary. In other words, downcycling concrete replaces aggregate and avoids landfilling, but doesn’t replace primary cement production.
How do circularity measures impact emissions in the cement & concrete sector?
Repair, reuse, recycling and downcycling measures in the concrete sector increase material efficiency and aim to preserve the value of the materials produced for a longer period of time. Through repair, reuse and recycling the demand for newly produced cement could potentially be reduced and with it, emissions coming from the cement sector. These measures can also help slow down the accumulation of construction waste in dedicated landfills [x].
​
Circularity measures in cement and concrete can have beneficial environmental impacts - but may not influence emissions from the sector in the short term.
​
However, recycling is still dependent on primary production due to the quality of the materials obtained through the recycling and crushing processes. In other words, concrete re-use and recycling rates depend on the properties and the purity of the recovered materials. For instance, when good quality concrete is available, it could replace 20%-30% of the total aggregate in a new concrete mix, meaning that new aggregate and cement is still always needed for new structural materials [xvii].
Cement reuse and recycling can partially reduce greenhouse gas emissions and help slow the growth of emissions in the sector [xviii]. It is also worth noting that any circularity measures in sectors such as construction will be dependent on demolishing concrete structures and building new ones at the same time and in the same area.
​
Most emissions in the concrete value chain occur during the production process of cement and will need to be reduced directly at the production sites to reach carbon neutrality. Overall, the climate impact of circularity measures in the cement and concrete sector will be case-specific [xix].
Clinker Substitution
Clinker is an intermediate product of cement made from heating limestone and clay (calcification) at temperatures around 1200°C. Usually mixed with gypsum to make concrete, it constitutes 73.7% of cement in the EU [xxi]. Production of clinker is the most energy and CO2 intensive part of the cement making process [xxii]. This is due to process emissions (resulting from the chemical reactions of the cement making process) as well as combustion emissions (energy input for heating, usually from fossil sources). Overall, the global average emissions intensity of clinker in 2019 was found to be 834 kg of CO2 per tonne of clinker [xxiii].
​
Substituting the amount of clinker to reduce its footprint by tackling process emissions is necessary, as the cement industry is not on track with global emissions reduction targets [xxiv].
​
Substituting clinker can be done with natural materials or industrial by products. Two widely used and technically mature substitutes are industrial by-products: fly ash which is a residue from coal plants, and blast furnace slag, a waste by-product of the steel making process. They bring about reductions in lifecycle emissions by 15-46% and 22-40% respectively [xxv,xxvi]. These substitutes provide material benefits but they are not sustainable in the long run with coal plants winding down and uptake of recycled steel.
​
Naturally occurring substitutes such as volcanic ash are possible sustainable alternatives that are nascent. For example, volcanic ash requires an assessment of scale as it is limited in its geographic availability. Calcined clay is both naturally occurring and an industrial by-product of paper sludge waste; studies show that this substitute could help the sector meet 2°C targets [xxvii].
​
The limitations that surround all clinker substitutes fall into one or many of these broad categories that need to be taken into account when considering clinker substitution:
-
Geographic availability: Being geographically bound, substitution is viable within certain geographical boundaries, limiting scalability.
​
-
Long term sustainability: Alternatives are resources with supply limitations. The environmental footprints of these alternatives extend beyond emissions reductions.
​
-
Keeping cement standards: The amount of clinker that can be substituted is limited so as to not compromise the integrity of the final product.
​
-
Cost: Certain substitutes are more expensive than others, despite having a greater positive climate impact.
Key measures and enablers needed
-
In addition to circularity measures, the primary production of cement needs to be decarbonised.
​
-
To achieve large recycling rates, more efficient separation and treatment techniques are needed to produce a sufficiently pure and homogeneous material for new concrete production [xx].
​
-
Explicit plans for the management and sorting of construction and demolition waste are needed to reach higher material efficiency rates.
​
-
To improve the separation of materials on-site, mobile sorting units and dedicated facilities are needed.
​
-
Designing buildings and infrastructure to retain the value of the materials and enable the repair of the structure can also have a positive impact. In addition, designing buildings to allow for future adaptations and enable simple deconstruction can help in the deconstruction and sorting process at the end-of-life of the concrete structure [x].
​
-
Even though developing a functioning infrastructure for high-value secondary concrete might be costly, once it is established, higher recycling rates are possible.
​
-
For promoting substitution of clinker, alternatives that are geographically limited must be recognised and promoted.
​
-
Assessing the availability of alternatives to clinker and the possible scale of utilisation are needed to ensure its efficient uptake.
​
Climate score
4/10
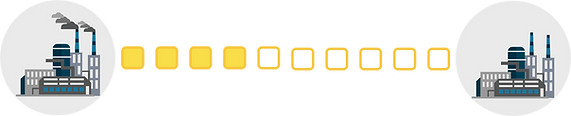
Climate change mitigation
The climate impact of circularity measures in the cement and concrete sectors varies on a case-by-case basis. The repair, reuse and recycling of concrete can bring environmental benefits, but can have technical limitations and may cause additional emissions (e.g., due to the transport of heavy materials).
6/10

Resource efficiency
Extending the lifetime of existing concrete structures, reusing them and recycling them after their use can significantly contribute to material efficiency in the built environment. However, obstacles in timing (e.g., demolition vs. building) and separation of materials prevent efficiencies as high as in the steel sector.
5/10
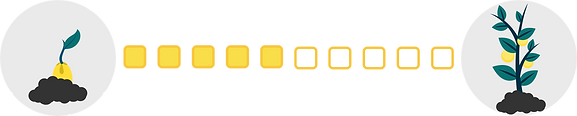
Deployment readiness
While concrete downcycling is common practice in the construction sector, repairing, reusing and recycling concrete and cement is not as common. Some pilot projects in the Netherlands and Denmark lead the way in deployment, but more projects and planning are needed to use concrete and cement more efficiently. In addition, long lifetimes (80+y) mean any design for reusability now will not have a potential benefit for a long time.
References
[[i] Gagg, Colin R. 2014. Cement and concrete as an engineering material: An historic appraisal and case study analysis. Engineering Failure Analysis 40: 114-140. Available at: https://doi.org/10.1016/j.engfailanal.2014.02.004
[ii] Benghida, D. 2016. CO2 reduction from cement industry. Advanced Materials, Mechanical and Structural Engineering – Hong, Seo & Moon (Eds) © 2016 Taylor & Francis Group, London, ISBN: 978-1-138-02908-8
[iii] Chatham House. 2018. Making Concrete Change: Innovation in Low-carbon Cement and Concrete. Available at: https://www.chathamhouse.org/2018/06/making-concrete-change-innovation-low-carbon-cement-and-concrete-0/executive-summary
[iv] BBC. 2018. Climate change: The massive CO2 emitter you may not know about. Available at: https://www.bbc.com/news/science-environment-46455844
[v] Kumar et al. 2021. A study on repair of concrete structure using non-destructive tests. Materials Today: Proceedings. Available at: https://doi.org/10.1016/j.matpr.2021.06.414
[vi] Bowyer et al. 2016. Atmospheric carbon dioxide and Premature deterioration of steel-reinforced Concrete structures – a growing concern. Available at: https://www.dovetailinc.org/upload/tmp/1579728946.pdf
[vii] Gebregziabhier, Tekeste Teshome. 2008. Durability problems of 20th century reinforced concrete heritage structures and their restorations. Masters Dissertation for Advanced Masters in Structural Analysis of Monuments and Historical Constructions, SAHC. Available at: https://core.ac.uk/download/pdf/41798104.pdf
[viii] VTT. 2014. Re-use of structural elements; Environmentally efficient recovery of building components. Available at: https://www.vttresearch.com/sites/default/files/pdf/technology/2014/T200.pdf
[ix] WBSCD. 2009. Recycling Concrete. Available at: https://www.wbcsd.org/contentwbc/download/2410/29973
[x] The Concrete Centre. 2021. End of life recycling. Available at: https://www.concretecentre.com/Performance-Sustainability-(1)/Material-Effieciency/End-of-life-recycling.aspx
[xi] Climate-KIC. Start-ups: SmartCrusher. Available at: https://www.climate-kic.org/start-ups/smart-crusher/
[xii] Slimbreker. The SmartCrusher Quarry 2020. Available at: https://www.slimbreker.nl/downloads/The%20SmartCrusher%20Quarry%202020.pdf?20190121
[xiii] Cement.org. 2019. Recycled Aggregates. Available at: https://www.cement.org/learn/concrete-technology/concrete-design-production/recycled-aggregates
[xiv] Recycling Today. 2020. Research shows recycled concrete can outperform traditional construction. Available at: https://www.recyclingtoday.com/article/recycled-concrete-university-british-columbia-research/
[xv] Cembureau. 2016. Cement, concrete & the circular economy. Available at: https://circulareconomy.europa.eu/platform/en/knowledge/cement-concrete-circular-economy
[xvi] ProCrewSchedule. 2020. Reusing and Recycling Concrete for Sustainable Construction. Available at: https://www.procrewschedule.com/reusing-and-recycling-concrete-for-sustainable-construction/
[xvii] European Concrete Platform ASBL. 2009. Sustainable benefits of concrete structures. Available at: https://www.theconcreteinitiative.eu/images/ECP_Documents/SustainableBenefitsConcreteStructures_EN.pdf
[xviii] Material Economics. 2018. The Circular Economy - a Powerful Force for Climate Mitigation. https://materialeconomics.com/publications/the-circular-economy-a-powerful-force-for-climate-mitigation-1
[xix] Mostert et al. 2021. Climate and resource footprint assessment and visualization of recycled concrete for circular economy. Resources, Conservation and Recycling Volume 174, November 2021, 105767. Available at: https://doi.org/10.1016/j.resconrec.2021.105767
[xx] European Concrete Platform ASBL. 2009. Sustainable benefits of concrete structures. Available at: https://www.theconcreteinitiative.eu/images/ECP_Documents/SustainableBenefitsConcreteStructures_EN.pdf
[xxi] Cembureau, 2018. Clinker substitution. Available at: https://lowcarboneconomy.cembureau.eu/5-parallel-routes/resource-efficiency/clinker-substitution/
[xxii] UN Climate Technology Center and Network, Clinker Replacement. Available at: https://www.ctc-n.org/technologies/clinker-replacement
[xxiii] GCC Association, GNR project. Available at: https://gccassociation.org/gnr/
[xxiv] IEA, Cement. Available at: https://www.iea.org/reports/cement
[xxv] Crossin, Enda. The greenhouse gas implications of using ground granulated blast furnace slag as a cement substitute. Journal of Cleaner Production 95 (2015): 101-108.
[xxvi] Elisabete R. Teixeira, Ricardo Mateus, Aires F. Camões, Luís Bragança, Fernando G. Branco, Comparative environmental life-cycle analysis of concretes using biomass and coal fly ashes as partial cement replacement material, Journal of Cleaner Production, Volume 112, Part 4, 2016, Pages 2221-2230, ISSN 0959-6526. Available at: https://doi.org/10.1016/j.jclepro.2015.09.124.
[xxvii] Waugh, Rachel & Pauliuk, Stefan & Allwood, Julian & Müller, Daniel. (2013). The Roles of Energy and Material Efficiency in Meeting Steel Industry CO2 Targets. Environmental Science and Technology. 47. 3455-3462. 10.1021/es3031424.
​
​